Products
PLdoser
PL series concrete batching machine is a kind of foreground automatic batching equipment used with mixer.
Key words:
Key words:
PLdoser
Details

This equipment is universal for large, medium and small mixing stations in various industries. It is mainly used for quantitative distribution of concrete or various fertilizers.

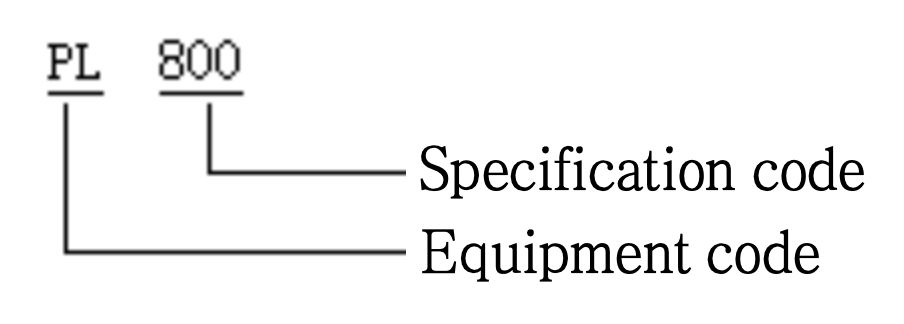

Dosing accuracy is better than ±2%;
The number of materials that can be dispensed: 2~5 kinds.
Feeding belt speed: 1.0~3.0m/s.
It can be freely combined into ideal products according to requirements;
High degree of automation and simple operation;
Accurate weighing, high dosing precision, high distribution efficiency.
Good stability, easy to use and maintain.
Ambient temperature: -10℃~50℃;

Equipment Model |
PL400 |
PL600 |
PL800 |
PL1200 |
PL1600 |
PL2400 |
Hopper capacitym³ |
0.4 |
0.6 |
0.8 |
1.2 |
1.6 |
2.4 |
Silo capacitym³ |
2×1.5 |
2×1.8 |
2×2 |
2×2.2 |
4×5 |
4×8 |
Dosing capacitym³/h |
28 |
32 |
48 |
60 |
75 |
120 |
Dosing accuracy% |
±2 |
±2 |
±2 |
±2 |
±2 |
±2 |
Maximum weighing valuekg |
1000 |
1500 |
2000 |
3000 |
4000 |
4000 |
Number of materials available |
2 |
2 |
2 |
2 |
3 |
3 |
Feed Belt Speed m/s |
1.0 |
1.0 |
1.0 |
1.25 |
1.6 |
1.6 |
Equipment power kW |
2×2.2 |
2×3 |
3×4 |
3×4 |
4×5.5 |
4×7.5 |
Loading height mm |
1900 |
2000 |
2300 |
2500 |
2600 |
2900 |
Equipment weight kg |
1150 |
1500 |
2300 |
2900 |
4500 |
5800 |
Overall dimensions m |
2.3×1.6×1.8 |
6×1.6×2.8 |
6.4×1.6×3 |
6.6×2×3.2 |
9.9×2×3.2 |
9.9×2×3.3 |

/ |
Nominal volume of weighing hopper |
Hopper volume |
efficiency of production |
Dosing accuracy |
weighing value |
Loading height |
Measurement method |
Dosing method |
Unloading method |
total power |
Overall quality of the machine |
Overall Dimension(L×W×H) |
|
m³ |
m³ |
m³/h |
% |
kg |
mm |
/ |
/ |
/ |
kw |
kg |
mm |
PL500 |
0.85 |
0.74*2 |
≥30 |
±2% |
≤2000 |
2400 |
electronic balance |
pneumatic brake |
pneumatic brake |
|
|
3370*1500*2800 |
PL500C |
0.72 |
0.4*1 |
≥30 |
±2% |
≤2000 |
2400 |
electronic balance |
Electric belt conveyor |
Electric belt conveyor |
|
|
2650*920*920 |
PL600A |
0.69 |
2.24*2 |
≥30 |
±2% |
≤2000 |
2400 |
electronic balance |
Electric belt conveyor |
Electric belt conveyor |
|
1070 |
4606*1600*2560 |
PL800 |
0.72 |
3.3*2 |
≥48 |
±2% |
≤2000 |
2400 |
electronic balance |
Electric belt conveyor |
Electric belt conveyor |
6.6 |
|
5635*1740*2810 |
PL800A |
1.2/2 |
2.6*2 |
≥48 |
±2% |
≤2000 |
2400 |
electronic balance |
pneumatic brake |
Electric belt conveyor |
|
|
6000*1500*2900 |
PL800B |
1.2/2 |
2.6*2 |
≥48 |
±2% |
≤2000 |
2400 |
electronic balance |
pneumatic brake |
Electric belt conveyor |
|
|
6000*1500*2900 |
PL800C |
1.2/2 |
2.6*2 |
≥48 |
±2% |
≤2000 |
2400 |
electronic balance |
pneumatic brake |
Electric belt conveyor |
|
|
6000*1500*2900 |
PL1200 |
1.77/3 |
2.98*3 |
≥(60-72) |
±2% |
≤3000 |
2400 |
electronic balance |
pneumatic brake |
Electric belt conveyor |
|
|
7893*1600*2550 |
PL1200A |
2.47/4 |
2.98*4 |
≥(60-72) |
±2% |
≤3000 |
2400 |
electronic balance |
pneumatic brake |
Electric belt conveyor |
|
|
10506*1600*2550 |
PL1200B |
2.2 |
2.2*3 |
≥(60-72) |
±2% |
≤3000 |
2400 |
electronic balance |
Belt/pneumatic gate |
pneumatic brake |
|
|
9600*1952*3100 |
PL1200C |
1.1 |
3*3 |
≥(60-72) |
±2% |
≤3000 |
2460 |
electronic balance |
Electric belt conveyor |
Electric belt conveyor |
16 |
3950 |
8300*2000*2895 |
PL1200D |
1.1 |
3*4 |
≥(60-72) |
±2% |
≤3000 |
2400 |
electronic balance |
Electric belt conveyor |
Electric belt conveyor |
20 |
5200 |
11200*2000*2895 |
PL1200E |
1.1 |
3*4 |
≥(60-72) |
±2% |
≤3000 |
2460 |
electronic balance |
Electric belt conveyor |
Electric belt conveyor |
24 |
5500 |
11200*2000*2895 |
PL1200F |
0.47*4 |
2.98*4 |
≥(60-72) |
±2% |
≤3000 |
3600 |
electronic balance |
pneumatic brake |
Belt/pneumatic gate |
|
|
10506*1600*2550 |
PL1200G |
1.4 |
2.6*2 |
≥(60-72) |
±2% |
≤3000 |
3800 |
electronic balance |
pneumatic brake |
pneumatic brake |
|
|
9238*2175*3055 |
PL1200H |
1.9/3 |
2.48*3 |
≥(60-72) |
±2% |
≤3000 |
3800 |
electronic balance |
pneumatic brake |
Electric belt conveyor |
|
|
6000*1500*2900 |
PL1600 |
2.97/3 |
5.46*3 |
≥(75-80) |
±2% |
≤3000 |
2400 |
electronic balance |
pneumatic brake |
Electric belt conveyor |
7.5 |
6500 |
9300*2000*3150 |
PL1600A |
4.18/4 |
5.45*4 |
≥(75-80) |
±2% |
≤3000 |
2400 |
electronic balance |
pneumatic brake |
Electric belt conveyor |
7.5 |
8500 |
12400*2000*3150 |
PL1600B |
0.58*4 |
5.6*4 |
≥(75-80) |
±2% |
≤3000 |
2460 |
electronic balance |
pneumatic brake |
Belt/pneumatic gate |
|
|
12000*2000*3250 |
PL1600C |
1.6 |
4.5*3 |
≥(75-80) |
±2% |
≤3000 |
2400 |
electronic balance |
Electric belt conveyor |
Electric belt conveyor |
16 |
|
9660*3157*2300 |
PL2400 |
5.79/4 |
9.3*4 |
≥(120-145) |
±2% |
≤4000 |
2400 |
electronic balance |
pneumatic brake |
Electric belt conveyor |
11 |
9800 |
13850*2200*3718 |
PL2400A |
0.72*4 |
9.3*4 |
≥(120-145) |
±2% |
≤4000 |
2460 |
electronic balance |
pneumatic brake |
Belt/pneumatic gate |
7.5 |
8500 |
13930*2200*3970 |
PL3200 |
6.4 |
≥14.1*4 |
≥(160-192) |
±2% |
≤5000 |
3600 |
electronic balance |
pneumatic brake |
Electric belt conveyor |
|
|
1440*2850*4500 |
PL3200A |
1.15*4 |
14.1*4 |
≥(160-192) |
±2% |
≤5000 |
3800 |
electronic balance |
pneumatic brake |
Belt/pneumatic gate |
|
|
14400*2856*4500 |
PL4800 |
0.48 |
≥(18-25) |
≥280 |
±2% |
≤8000 |
3800 |
electronic balance |
pneumatic brake |
Belt/pneumatic gate |
|
|
14000×3000×4860 |
Basic knowledge: dry sand angle of repose 35 degrees, wet sand angle of repose 40 degrees, dry gravel 35-45, tailing sand (dry) 27-36; sand density 1.4-1.6, 1300-1600KG/m3.
Automatic completion of sand, stone, cement and other materials batching, by the storage hopper, weighing system, feeding system, electronic control system and other components. The feeding mode has pneumatic gate and belt conveyor.
Average funnel mouth under the material conveying speed (according to the continuous average to analyze): set the funnel mouth area of S, under the material speed of V, there are S * V * time = production rate m3, time 1 hour = 3600 seconds, inverse deduction can be known as under the material speed of V, V can be two kinds of units, one unit of MM / t, the other is KG / t, KG / t is a substitution of gravel density.
The study of PL soil mixer batching machine: the market has the following chart common types of PL batching machine (feeding mode pneumatic gate and belt conveyor conveyor two kinds), because the industry has no specific size specification, so many manufacturers produce the same type of mode and size are not the same, but the basic parameters of the principle is the same, as long as the basic parameters are the same as the same can be named as the same PLXX batching machine.
The most important parameters of PL batching machine are as follows: weighing hopper volume size, productivity, storage hopper volume size, falling material port size (storage hopper under the material area size), transport feeding port size (bucket feeding area size), the total length, width and height of the machine dimensions (taking into account the safety of transportation, the total height of not more than 2.9 meters), the industry of each type of size of the hopper volume size, productivity, storage hopper volume size, power are Is matched, the relevant parameters are also industry experience, is the people's long-term work in the valuable practice data dosage interval cycle 60 seconds / times.
Average funnel mouth under the material conveying speed (according to the continuous average to analyze): set the funnel mouth area of S, under the material speed of V, then there are S * V * time (S) = productivity m3 / H, time 1 hour = 3600 seconds, inverse deduction can be known as under the material speed V, V can be two kinds of units, one unit of MM / t, the other for KG / t, KG / t is a substitute for the density of sand and gravel.
Storage hopper feeding time required: (the longest time) for PL800 example: 48/0.8 = 60 times, 60 times 3600 S, (the longest time required 3600/60 = 60 S each time) Description of the longest time for a minute to weigh a bit, but the actual weighing of a bit of all the action is completed to the mixer in the total time, so the storage hopper feeding time should be 48 cubic meters of material in the hopper under the state of the average time required to finish the leakage in a continuous manner. The average time required to complete the state of leakage, according to the experiment to know, know the time (under the premise of a certain area), can also be calculated for the speed of the material V .
Average belt conveying speed: (800 * 1.6 = 1280, appropriate enlargement of 900 * 1.6 = 1440 <1500KG, each divided into 60 seconds, so 1440/60 = 24kg / min (a dosage process).
Related Products
Online message